What is Porosity in Welding: Key Factors and Their Influence On Weld High Quality
What is Porosity in Welding: Key Factors and Their Influence On Weld High Quality
Blog Article
The Science Behind Porosity: A Comprehensive Guide for Welders and Fabricators
Comprehending the detailed systems behind porosity in welding is important for welders and fabricators making every effort for impeccable craftsmanship. From the composition of the base products to the complexities of the welding process itself, a plethora of variables conspire to either worsen or relieve the visibility of porosity.
Comprehending Porosity in Welding
FIRST SENTENCE:
Assessment of porosity in welding exposes important insights into the honesty and high quality of the weld joint. Porosity, characterized by the presence of cavities or spaces within the weld steel, is a common problem in welding processes. These voids, otherwise effectively dealt with, can endanger the architectural integrity and mechanical residential properties of the weld, leading to prospective failings in the completed product.
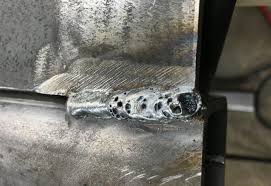
To spot and evaluate porosity, non-destructive testing techniques such as ultrasonic testing or X-ray evaluation are usually utilized. These techniques permit the recognition of internal problems without compromising the stability of the weld. By analyzing the size, form, and distribution of porosity within a weld, welders can make enlightened choices to boost their welding processes and attain sounder weld joints.
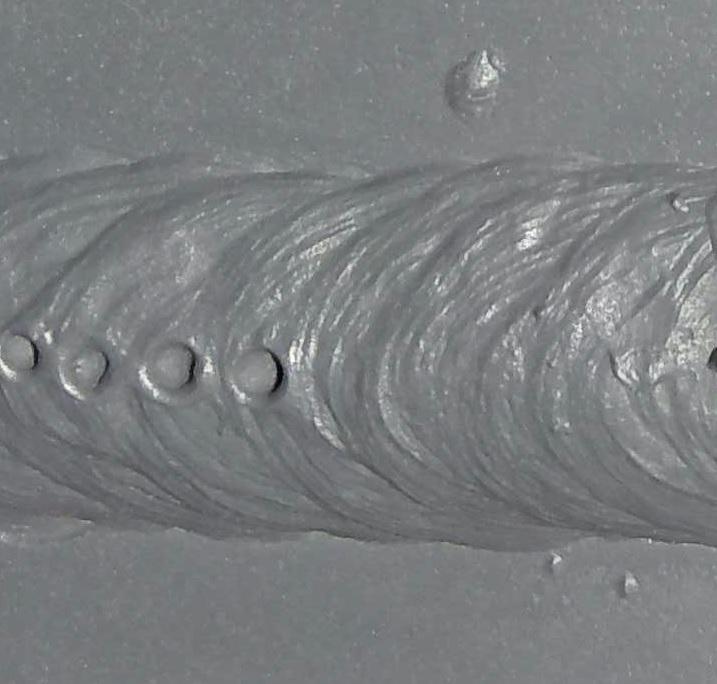
Aspects Influencing Porosity Development
The incident of porosity in welding is influenced by a myriad of elements, ranging from gas securing performance to the details of welding specification setups. Welding criteria, consisting of voltage, existing, take a trip speed, and electrode kind, also effect porosity development. The welding strategy employed, such as gas steel arc welding (GMAW) or protected steel arc welding (SMAW), site can affect porosity formation due to variants in heat distribution and gas coverage - What is Porosity.
Results of Porosity on Weld Top Quality
The visibility of porosity also deteriorates the weld's resistance to deterioration, as the entraped air or gases within the voids can respond with the surrounding setting, leading to degradation over time. Furthermore, porosity can impede the weld's capacity to endure pressure or effect, more jeopardizing the overall high quality and reliability of the bonded framework. In essential applications such as aerospace, automotive, or structural buildings, where security and longevity are critical, the harmful impacts of porosity on weld high quality can have serious repercussions, highlighting the significance of lessening porosity with appropriate welding methods and treatments.
Methods to Reduce Porosity
In addition, utilizing the appropriate welding criteria, such as the appropriate voltage, existing, and travel rate, is critical in avoiding porosity. Keeping a constant arc size and angle during welding likewise helps lower the possibility of porosity.

Using the suitable welding strategy, such as back-stepping or using a weaving activity, can additionally aid disperse warm evenly and decrease the chances of porosity formation. By implementing these strategies, welders can properly decrease porosity and produce top quality welded joints.
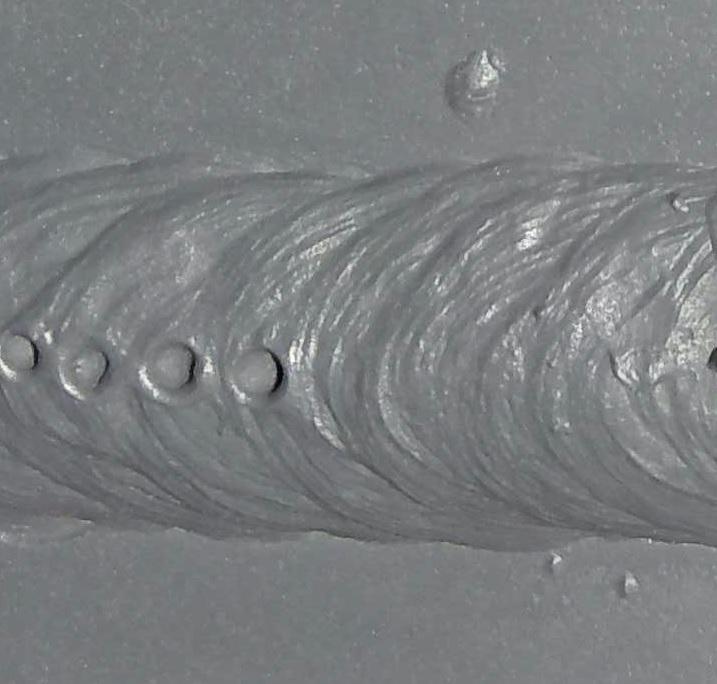
Advanced Solutions for Porosity Control
Executing sophisticated innovations and cutting-edge techniques plays a crucial function in attaining superior control over porosity in welding processes. In addition, employing innovative welding strategies such as pulsed MIG welding or go to this site modified ambience welding can additionally help reduce porosity problems.
One more sophisticated service involves making use of advanced welding devices. For circumstances, making use of devices with integrated functions like waveform control and sophisticated source of power can enhance weld high quality and reduce porosity risks. The implementation of automated welding systems with exact from this source control over specifications can substantially reduce porosity flaws.
In addition, integrating innovative surveillance and examination modern technologies such as real-time X-ray imaging or automated ultrasonic screening can help in detecting porosity early in the welding process, permitting instant rehabilitative actions. On the whole, integrating these innovative options can considerably boost porosity control and boost the general high quality of bonded components.
Verdict
In final thought, understanding the science behind porosity in welding is important for welders and makers to produce high-grade welds - What is Porosity. Advanced options for porosity control can further boost the welding procedure and make certain a solid and reputable weld.
Report this page